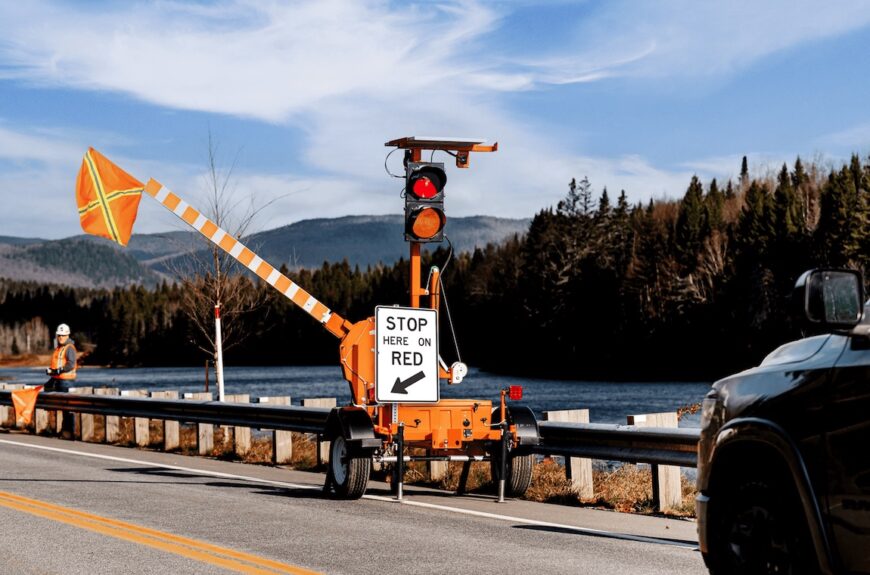
Smart Work Zone Technology FAQs
How innovation saves money, decreases accidents and helps traffic flow smoother
The below AWP Safety article was also feature in Roads & Bridges during National Work Zone Awareness Week.
Let’s be honest — managing a road construction site is no walk in the park. Between traffic control, worker safety and meeting deadlines, project managers have a full plate. But here’s the good news: Technology is stepping in to make the job easier (and work zones safer).
Adapting to innovation isn’t easy. Project managers and other decision-makers ask a lot of questions as they test new technology. In recognition of National Work Zone Awareness Week, let’s tackle some frequently asked questions about how technology can transform your work zones.
“Sounds complicated. Do I really need tech in work zones?”
Think about it like this: Would you still use paper maps to navigate your way to a job site? Probably not. Everyone uses GPS. Work zone technology is just another upgrade, designed to keep workers safer, improve efficiency and—most importantly—help everyone go home at the end of the day.
Take wearable safety tech, for example. Sensor-equipped safety vests can track workers’ locations and send out alerts if they enter an unsafe area. That’s like having an extra set of eyes on every worker.
And here’s the kicker: Adopting work zone tech doesn’t mean ditching your experience and expertise. It’s about adopting better tools to do what you already do best—run a safe and efficient job site.
How do SMART WORK ZONES Actually Work?
Think of a smart work zone as a construction site that can “talk” to vehicles and traffic management teams. These zones might use sensors, cameras and AI-powered software to analyze traffic conditions and send real-time updates. Just consider these scenarios that play out in work zones everyday:
- If traffic is backing up, electronic signs can adjust speed limits or suggest detours without manual intervention.
- Connected vehicles can receive work zone alerts, giving drivers advance notice to slow down (maybe you’ve already experienced this using your smartphone’s navigation app).
- Managers can monitor traffic patterns and adjust staffing or equipment use based on changing conditions, using real-time data.
Also notable: A study led by the United States Department of Transportation (USDOT) has shown that Queue Warning Systems (QWS)—one of the most commonly deployed technologies in work zones today—reduce the potential for rear-end crashes by 18% to 45% on work zone approaches.
Using real-time data from sensors, these systems manage traffic by informing drivers of downstream conditions, meaning motorists can be alerted and adjust their driving before reaching a congested area.
Some smart work zone innovations remain in the research phase, others in the lab, but many are actively deployed, helping to create safer, more efficient construction environments.
Do Automated Flagger Assistance Devices (AFADs) actually improve safety?
AFADs take human flaggers out of harm’s way. Instead of a person standing in traffic, AFADs use high-visibility stop-and-go signals, sensors and cameras to manage vehicle flow. A trained worker controls them remotely from a safer position. Here’s what makes them a game-changer:
- They eliminate human fatigue and distraction. A flagger on hour-six of a hot day isn’t as sharp as one on hour-one. AFADs are always at 100%.
- They reduce accident risk. The Missouri Department of Transportation found that motorists were more responsive to AFADs and that 78% of drivers prefer AFADs over human flaggers.
Bottom line: if you’re looking for a safer, more consistent way to manage traffic in work zones, AFADs are a solid investment.
Can technology actually save me money?
Absolutely. Let’s break it down. Fewer accidents mean lower insurance and legal costs. Less downtime means projects stay on schedule (and budget). Smarter traffic flow gives project managers fewer delays and fewer penalties for missed deadlines.
The return on investment for adopting smart work zone technologies will vary depending on the task, the terrain and the tools used. But what’s clear is that it has the power to enhance safety, optimize efficiency and prevent costly project overruns, making it an investment that can quickly pay for itself not just in terms of dollars, but also days spent safely on the job.
Where’s the easiest place to start if I’m on the fence?
If you’re unsure about integrating technology into your work zones but want to take a step in the right direction, Traffic Monitoring Devices (TMDs) like intelligent traffic cones are a great first step.
These devices provide traffic data to help managers make informed decisions about lane closures, congestion control and worker safety without requiring major infrastructure changes or extensive training. Here’s why crews love them:
Easy setup – most intelligent cones (and barrels) are designed for quick deployment. Unlike traditional traffic data collection methods that require permanent sensor installations or underground loops, these devices are portable (most can be set up in minutes). Simply place them near a work zone, and they start collecting data instantly.
Solar-powered – modern TMDs tend to operate on solar power with battery backup, eliminating the need for frequent maintenance or external power sources. This self-sustaining energy system ensures continuous operation even in remote or off-grid locations.
Packed with data – these devices track how fast vehicles are moving through a work zone. They identify areas where sudden slowdowns could lead to rear-end collisions, recognize peak traffic times and plan lane closures accordingly to minimize disruptions. The devices also can detect patterns such as abrupt braking or erratic lane changes, which may indicate unsafe conditions.