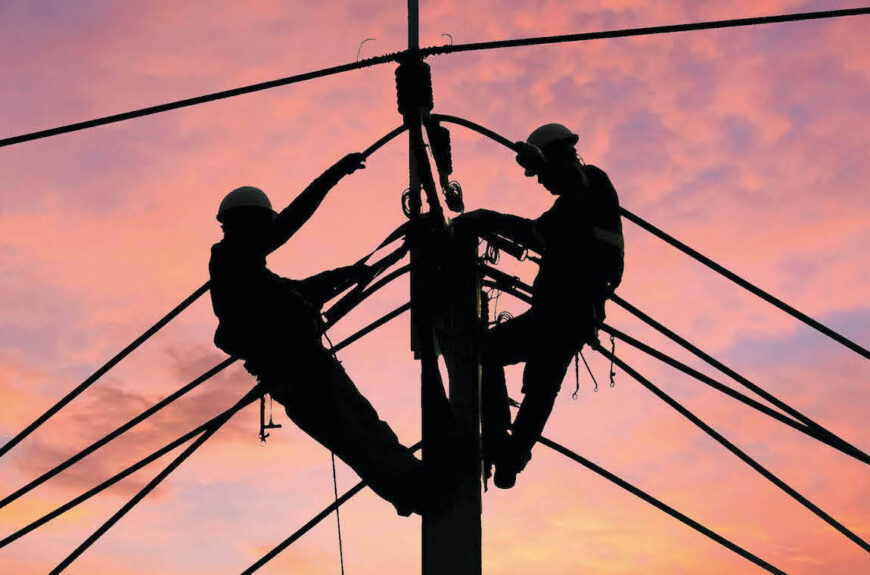
Safety Culture + Technology Create Safer, More Productive Worksites
Utility construction activity is way up. A U.S. Census Bureau survey reports public electric power agency spending jumped 56% between October 2022 and October 2023 alone. Spending was also up in wastewater and water supply categories. These infrastructure upgrades are great for communities and businesses, but introduce more possibilities for potential worksite accidents as more crews are deployed to more locations. Utility and construction companies that partner with process- and data-driven suppliers can improve crew safety and cover more jobs in less time.
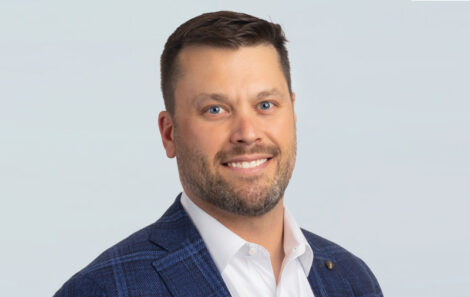
Q: When it comes to safety, what differentiates high-performing companies from the rest?
I’ve worked within the utility and construction space for nearly 20 years, and have seen first-hand that safety is one of the greatest challenges for any company operating in a field service environment. Those that do it well have three characteristics.
First is having a strong safety culture. For AWP Safety, that means having extremely high levels of safety engagement and support from the C-suite to our Protectors working directly with utility and construction crews. We make the analogy that bringing a safety mindset to work is like remembering to wear pants. It’s something you do every day.
Second is having a Safety Management System (SMS) that standardizes processes and creates rigor around safety training and deployment. An SMS establishes consistent expectations for everyone and outlines the specific actions we expect from our team members.
Finally, using technology to gather and analyze data gives companies insights into how they’re performing relative to their SMS.
Q: How do you use technology to improve the safety of AWP Safety customers?
We are strategic about the technology we use, and utilize multiple tools to improve the safety of our customers’ and our own work crews. Since our work is fleet intensive, vehicle telematics is crucial for us. We use a technology called Samsara that provides visibility into the driving habits of team members using AWP safety trucks on the job. Based on the data, we can help our drivers make positive adjustments which helps prevents accidents. It’s also helped us reduce truck idle time, improve fuel efficiency and take a more proactive approach to fleet maintenance. These are operational improvements on our end that translate to greater worksite coverage and lower risk and liability for our customers.
We also incorporate tools like Intelex that capture data from audits and observations. This lets us monitor for improvements in the customer experience, determine the root cause of incidents and identify proactive adjustments.
Q: How can companies translate data into performance improvements?
At AWP Safety, we say that “if we don’t know better, we can’t do better.” Data helps us identify improvement opportunities, but what we DO with the data is what really counts. The data helps empower our leaders to target those improvement areas based on SMS policies, procedures and training we already have place. This approach has helped us achieve an industry-leading total recordable injury rate.
Q: Do you have any specific examples?
Absolutely. We’ve seen how great safety communication and training improves safety even during times of rapid growth. Last year, we grew our team in Las Vegas by 10 times and still achieved zero recordable injuries at that location. In Arizona, we had 130 drivers achieve impressive scores of 98 out of 100 in their safety metrics. We are proud of these teams and regularly share accomplishments like this enterprise-wide. The recognition motivates everyone to operate more safely.
Q: How does safety improve productivity? Are they related?
It comes down to planning. Whether it’s a major infrastructure project or something simpler like replacing a couple transformers, a planned job is always going to be safer and more productive. Inviting safety experts to the table early in the process means we can plan ahead for the right people and equipment, and the best worksite coverage. Here’s an example. It’s safer and more productive to close an entire road temporarily so a line crew can easily work their way down the road to make multiple repairs, instead of setting up separate, multiple worksites on that same road throughout the day. There will be a lower risk of vehicle accidents, and the line crews will probably complete their work faster. It’s a win-win, for safety and productivity.
Learn more about AWP Safety innovations and our commitment to safety.